Off the rack insulation products are useful in many consumer applications because they are often designed to a specific standard or end use. The most common example of this is wall insulation for residential and commercial buildings, which are produced in widths that match standard code for wall stud spacing. With industrial applications, the flexibility of custom production gives manufacturers a competitive and economic advantage. For example...
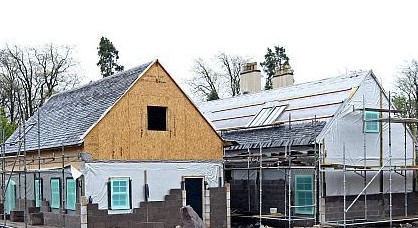
Housewrap
Anybody who has swung a hammer for Habitat for Humanity, or been anywhere near a home remodel, knows about housewraps. These products, which are required by most building codes, protect buildings from water intrusion and air infiltration while allowing moisture vapor to exit the building envelope. This improves energy efficiency and prevents mold and mildew growth within the wall cavity. Sigma was approached by a Fortune 500 producer of building products with a radical idea: a high-performance housewrap that also added R-value.
The obvious solution was to incorporate a durable low emissivity (low-e) layer with the customer’s existing product. This turned out to be a major challenge. Laminating their product to a low-e film would eliminate the breathability housewrap products require. Earlier attempts by the client lacked Sigma’s corrosion protection, and the low-e components were too easily corroded in the presence of rainwater and humid air. A protective coating over the low-e layer could solve this problem. Unfortunately, conventional roll coating techniques were not capable of protecting the aluminum without clogging the pores within the housewrap and substantially reducing the reflective properties of the low-e layer.
Sigma incorporated its VaporPhase Deposition and SigmAlOx™ technologies to protect the low-e layer from corrosion and oxidation without impacting product breathability, resulting in an insulation product with all the intrinsic benefits of a best-in-class protective housewrap. Ultimately, this joint effort resulted in a family of patents, technology licenses, and a world class coating facility commissioned by Sigma within the customer’s facility.
RV and Mobile Home Insulation
The challenge with mobile homes and RVs is that they need to be light and compact while simultaneously remaining comfortable in different climates. The industry has responded to these difficulties by installing radiant barriers in the roof and walls of the vehicle. Conventional radiant barrier products are made with aluminum foil or metalized film laminated to a high-strength scrim or fabric. This is a problem in cases where space is shared with electrical wiring because uncoated (or poorly coated) aluminum is highly conductive. Most laminated radiant barriers are also heavy (up to 30 lbs per 1000 sq ft), require seaming to meet wide width requirements (usually no wider than 51 inches), and are susceptible to oxidation and corrosion (losing reflectivity when exposed to heat and humidity). All of this leads to a product that can be safety risk, is difficult to install, and may not perform during the useful life of the vehicle.
Moving away from these products opens the possibility of products that are thinner and lighter, stronger, longer lasting, significantly less conductive, and easier to install. Sigma combined various technologies within its portfolio to capitalize on all of these possibilities - it developed a product that is 33% lighter, 50% stronger, less conductive, highly resistant to oxidation and corrosion over time, and is available in seamless widths up to 98 inches (a perfect width for most recreational vehicles).
Hot Tubs and Spas
Manufacturers of hot tubs and spas, like Maax Spas and Jacuzzi, use special reflective insulation around the walls of their spas to reflect back in the heat to make the spa more efficient. Low-emissivity reflective insulation is optimal here for a number of reasons.
First, hot tubs generate a lot of heat and humidity. Traditional fibrous insulation materials lose insulation value as they absorb moisture. While low emissivity insulations do not absorb moisture, many low emissivity aluminum products corrode in high heat and humidity. As a result, they need something that's not only high insulating and low emitting, but also highly resistant to corrosion from humidity. This means either a specialty coating over the aluminum that prevents corrosion in even the most extreme circumstances, or using a metal other than aluminum which would be naturally corrosion resistant.
Second, hot tubs also generate a large amount of heat and have very little space to insulate against it. In small spaces at high temperatures, low emissivity reflective insulation can actually achieve a higher insulation value per inch than fibrous and even some foam insulations. For example, in 1/4 inch space, with the internal temperature at 104F, the insulation value is about R-1.3, which comes to R-5.2 per inch - compared to fiberglass at about R-3 per inch and high-density EPS foam at about R-4 per inch.